In the medical device industry, ensuring product safety and compliance starts with robust packaging testing. Packaging is not only about protecting a device but also about maintaining sterility, integrity, and performance under various conditions.
In this article, we’ll explore the key testing methods and protocols used to validate medical device packaging, from seal strength tests to distribution simulations, providing a complete overview of the process that helps keep patients safe and products compliant. Whether you’re new to medical device manufacturing or seeking to enhance your understanding of packaging requirements, this guide will equip you with the knowledge needed to navigate the complex world of medical device packaging testing.
Key Components of Medical Device Packaging Testing
The first step in understanding medical device packaging validation testing is to familiarize yourself with its key components. Each component addresses a specific aspect of packaging integrity, ensuring that medical devices remain sterile, secure, and fully functional from production to end use. Here are the primary elements involved in the process:
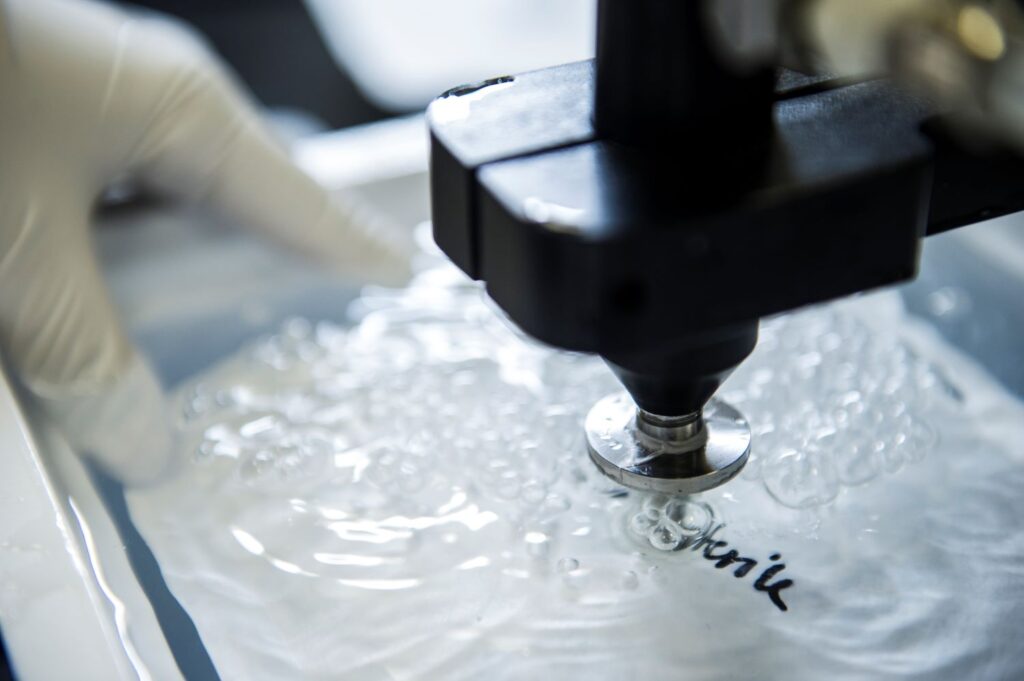
- Sterile Barrier Systems:
The sterile barrier system is the foundation of any medical device packaging solution. This system protects the device from contamination and preserves sterility. Testing ensures that these barriers can withstand environmental and physical stresses, preventing any potential breaches that could compromise product safety. - Seal Strength Testing:
Ensuring strong, reliable seals is essential for maintaining the integrity of the packaging. Seal strength testing, governed by standards like ASTM F88, assesses whether the packaging seals can endure handling, transport, and storage without failing. Methods such as peel testing help verify that seals can resist external forces that might otherwise allow contaminants to enter. - Environmental Condition Testing:
Medical device packaging must perform reliably under various environmental conditions. Environmental testing, which can involve temperature cycling, humidity exposure, and pressure testing, helps simulate real-world scenarios that the packaging may encounter. These tests ensure that materials maintain their protective qualities in diverse climates and storage conditions, including those encountered during international transportation. - Material and Biocompatibility Testing:
The materials used in packaging are tested for durability, flexibility, and compatibility with the device. Biocompatibility testing confirms that the materials are safe for direct or indirect contact with the medical device. Accelerated Aging standards like ASTM F1980 guide testing to ensure that materials do not degrade over time or under stress, maintaining the packaging’s protective qualities throughout its shelf life. - Package Integrity and Leak Testing:
This type of testing identifies any weaknesses or leaks that could compromise the sterile barrier system. Common methods include dye penetration testing (ASTM F1929) and bubble leak testing (ASTM F2096), which detect even minor flaws that might otherwise go unnoticed. Ensuring package integrity is crucial for protecting devices from contamination during their lifecycle. - Packaging DistributionTesting:
Simulating transportation conditions, such as shocks, vibrations, and compression, is essential for assessing how well the packaging protects the device during shipping. Standards like ASTM D4169 outline the steps for transportation simulation, helping verify that packaging can endure the stresses associated with distribution without compromising device safety.
By understanding these key components, medical device manufacturers can better prepare their products for the demanding requirements of the healthcare industry. These testing protocols not only ensure compliance with regulatory standards but also contribute to the overall safety and reliability of medical devices in the hands of healthcare professionals and patients.
Comprehensive Medical Device Packaging Testing Procedures
Having covered the key components, it’s important to dive deeper into the comprehensive testing procedures involved in medical device packaging validation. These procedures ensure that packaging systems can withstand various stresses and protect devices under a range of conditions.
Listed below are some of the most important testing procedures in the industry:
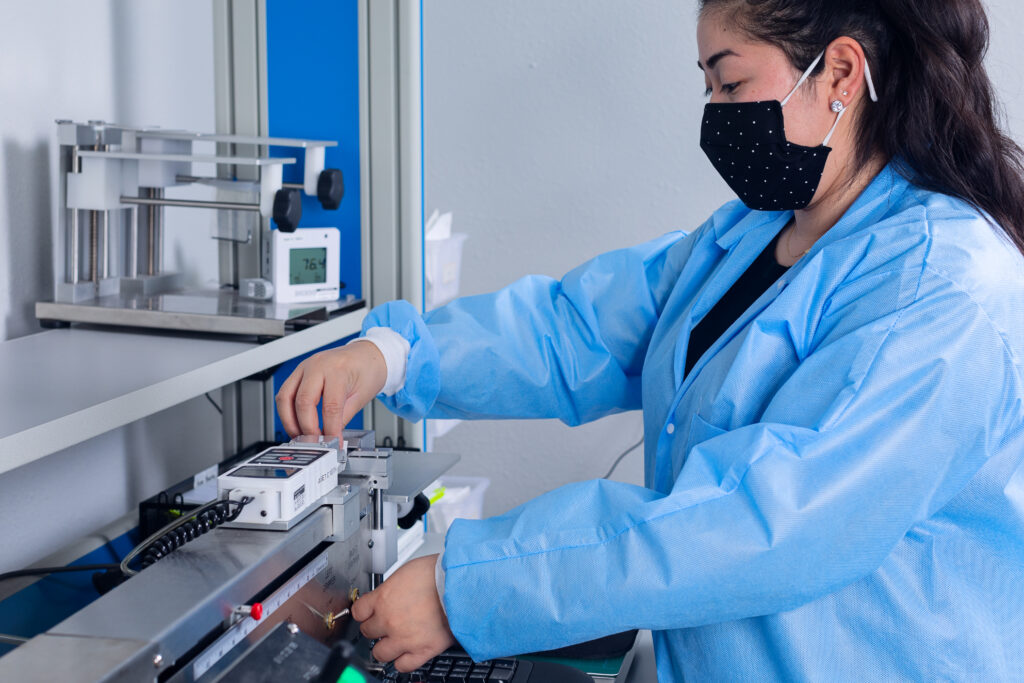
- Seal Integrity Testing:
Seal integrity testing is critical for validating that the seals on medical device packaging are robust enough to maintain sterility throughout the product’s lifecycle. Common methods include burst testing, which measures the pressure at which seals fail, and peel testing, which assesses the force required to separate seals. By evaluating seal strength under different conditions, manufacturers can confirm that seals will withstand physical stresses during transport and handling. - Package Integrity Testing:
Ensuring package integrity is vital for preventing contamination. Dye penetration testing (ASTM F1929) is widely used to detect leaks in porous packaging materials. This test involves applying a dye to one side of the packaging and inspecting the other side for any signs of penetration. Another common method is bubble leak testing (ASTM F2096), where packaging is submerged in water, and a vacuum is applied to detect leaks through the presence of bubbles. These tests are fundamental for confirming the sterile barrier system’s effectiveness. - Environmental Conditioning and Aging Tests:
Medical device packaging must endure storage environments over extended periods without degradation. Environmental conditioning tests simulate factors like temperature cycling and humidity exposure to evaluate how well the packaging materials maintain their integrity. ASTM F1980 provides guidelines for accelerated aging tests, which help predict the packaging’s performance over time. These tests are critical for establishing the shelf life of packaging materials and ensuring they meet storage requirements. - Packaging Distribution Testing:
Packaging must protect the device from physical damage during shipping. ASTM D4169 outlines procedures for packaging distribution testing, which replicates conditions such as drops, vibration, and compression. Drop testing involves dropping the packaged device from specified heights to observe potential damage, while vibration tables simulate the continuous motion that can occur during transportation. These tests help ensure that packaging systems are resilient enough to handle the rigors of shipping and distribution. - Material Testing and Compatibility Assessments:
Testing the packaging materials for durability and biocompatibility is essential for confirming their suitability for medical devices. Tests assess attributes like tensile strength, flexibility, and chemical resistance. Biocompatibility assessments ensure that materials do not pose any risks when in contact with the medical device. ASTM F3039 and other standards guide these tests to ensure materials maintain their protective qualities under different conditions. - Accelerated and Real-Time Aging Studies:
Accelerated aging studies simulate extended storage conditions in a shortened time frame to verify packaging durability over the intended shelf life. Real-time aging studies, on the other hand, involve storing packaging under normal conditions and periodically testing it over time. These studies are essential for determining the packaging’s long-term performance and ensuring it can maintain integrity until the end of its lifecycle. - Sterile Barrier System Testing:
Sterile barrier systems are rigorously tested to ensure they prevent microbial contamination. This includes sterility testing and assessments of the barrier’s physical properties under environmental conditions. Bubble leak testing and seal strength testing are often combined to validate the sterile barrier, ensuring that it can withstand handling, transportation, and storage without compromising sterility. - Performance and Functional Testing:
Performance testing evaluates the overall effectiveness of the packaging. This includes assessing how well the packaging supports device functionality, such as ease of opening without damaging the device, or how the packaging design facilitates proper usage by healthcare professionals. Functional testing ensures that the packaging not only protects but also enhances the usability of the medical device.
From initial design to final distribution, each testing method plays an important role in validating that medical device packaging can effectively protect devices and maintain compliance with regulatory requirements. These procedures provide peace of mind for manufacturers and healthcare providers alike, ensuring that every medical device reaches the patient safely and in optimal condition.
Types of Testing Facilities and Equipment Used in Medical Device Packaging Testing
Besides having a deep understanding of testing protocols, it is equally important to recognize the types of facilities and specialized equipment used in medical device packaging testing. These testing facilities are equipped with advanced technology to accurately simulate real-world conditions and thoroughly assess the durability and effectiveness of packaging systems.
- Environmental Chambers:
Environmental chambers are used to simulate a wide range of storage environments, allowing testers to control variables such as temperature, humidity, and pressure. These chambers are essential for accelerated aging tests and environmental conditioning, helping determine how well packaging materials hold up under various conditions. They are crucial for assessing shelf life and stability in compliance with standards like ASTM F1980. - Vibration and Shock Test Systems:
Vibration tables and shock test systems replicate the conditions a package might experience during transportation. Vibration tables simulate continuous movement, while shock test systems replicate impacts such as drops and bumps. These systems help evaluate packaging resilience, ensuring that the device remains protected through every stage of the distribution environment. - Seal Strength and Burst Testers:
Seal strength and burst testers are specialized machines that assess the strength and integrity of package seals. They can measure the force required to peel or burst seals, validating that they are robust enough to maintain sterility under physical stress. ASTM F1140 and ASTM F2054 outline the standards for these tests, ensuring the packaging’s seal strength meets industry requirements. - Leak Detection Equipment:
Leak detection tools, including dye penetration testers and bubble leak testers, are used to identify potential weaknesses in the packaging. Bubble leak testers, for example, can detect even the smallest leaks by submerging the package in water and applying a vacuum, while dye penetration testers apply a dye solution to confirm the integrity of porous packaging. These tests are essential for sterile barrier system validation. - Material Testing Machines:
Material testing machines evaluate packaging materials for properties such as tensile strength, flexibility, and chemical resistance. They confirm that materials can withstand physical stress without breaking down or compromising the device’s safety. Equipment for tensile testing, for instance, ensures that the packaging material can stretch and resist tearing during handling and transportation. - Biocompatibility and Chemical Testing Labs:
Biocompatibility labs evaluate packaging materials for any adverse chemical reactions that could occur upon contact with the medical device. These labs are equipped to perform tests that ensure the materials are safe for use and comply with regulations on biological evaluation. This testing is essential for packaging that directly contacts medical devices or patients.
Once all the necessary testing is complete, medical device packaging must meet regulatory requirements before it can be approved for market release. Compliance with regulations is important for both the safety and effectiveness of the packaging as well as for meeting the legal standards set by governing bodies.
Regulatory Compliance in Medical Device Packaging Testing
Regulatory authorities, such as the U.S. Food and Drug Administration (FDA) and the European Medicines Agency (EMA), establish strict guidelines for medical device packaging. These agencies mandate that all packaging systems undergo extensive testing to verify that they maintain sterility, integrity, and effectiveness throughout the product’s lifecycle. Compliance with standards like ISO 11607 and ASTM guidelines ensures that medical device packaging can consistently perform as required under various conditions. Here’s how compliance factors into the overall testing process:
- ISO and ASTM Standards:
ISO 11607 is a widely recognized standard for medical device packaging, covering requirements for terminally sterilized medical devices. It provides comprehensive guidelines for packaging design, validation, and documentation, ensuring that all aspects of the packaging process meet industry benchmarks. ASTM standards, such as ASTM F1980 for accelerated aging and ASTM F2096 for leak testing, offer specific methods for validating packaging performance. Adherence to these standards is critical for regulatory approval. - Validation and Documentation:
Regulatory bodies require thorough documentation for each testing phase, from seal integrity to environmental conditioning. This documentation must demonstrate that the packaging systems have passed all required tests and meet the specifications outlined in relevant standards. Validation reports provide proof of compliance and support regulatory submissions, ensuring that medical devices can be legally marketed and sold. - Risk Management and Quality Assurance:
Risk management is integral to the medical device packaging testing process. By identifying potential risks, such as contamination or physical damage, manufacturers can implement measures to mitigate these risks and improve packaging reliability. Quality assurance teams work alongside testing facilities to monitor each step of the testing process, ensuring that all results are accurate, consistent, and compliant with regulations. - Ongoing Compliance and Monitoring:
Even after regulatory approval, manufacturers must continue to monitor their packaging systems for compliance. Regular testing, process validation, and quality audits help ensure that packaging systems remain effective and compliant throughout the product’s lifecycle. This ongoing monitoring is essential for maintaining certification and meeting evolving industry standards.
Conclusion
With these testing procedures and regulatory requirements in place, medical device manufacturers can confidently bring their products to market, knowing that they have met all necessary safety and performance benchmarks.
In a constantly evolving industry, ongoing compliance and monitoring are the only ways to maintain product certification and meet emerging standards. Whether you are a seasoned professional or new to the field, understanding and implementing robust packaging testing protocols are fundamental steps in delivering safe, effective, and compliant medical devices.
At Pro-Tech Design & Manufacturing, we support clients through every step of this process, from initial testing to regulatory submission. Through robust testing and careful adherence to regulations, we help medical device companies deliver safe and reliable products to healthcare providers and patients worldwide.
For more information on our complete package testing services and our in-house ISO 17025-certified laboratory, please contact Pro-Tech Design & Manufacturing today.
FAQ
- What is the purpose of medical device package testing?
Medical device package testing ensures that the packaging systems can withstand environmental stresses, transportation, and storage without compromising sterility or safety. This testing is essential for preventing contamination and physical damage to the device.
- What are some common medical device packaging testing methods?
Common methods include seal strength testing (ASTM F1140), dye penetration testing (ASTM F1929), distribution testing (ASTM D4169), and stability testing. These methods assess different aspects of packaging performance, such as integrity, strength, and durability.
- Why is environmental condition testing important in medical device packaging?
Environmental condition testing evaluates how the packaging holds up under various climate conditions, including temperature fluctuations and humidity. This is crucial for ensuring that packaging systems can handle real-time environmental stresses without compromising the device’s sterility.
- What role does ASTM F1980 play in medical device packaging testing?
ASTM F1980 provides guidelines for accelerated aging tests, which help determine the shelf life of packaging materials. This is vital for verifying long-term durability and performance, allowing companies to estimate how packaging will perform over time.
- How does distribution testing help in medical device packaging?
Distribution testing replicates conditions that the packaging might experience during transit, such as vibration, compression, and drop impacts. This testing is crucial for identifying any potential risks of packaging failure during shipment, helping ensure the device arrives safely at its destination.
- What are the regulatory requirements for medical device packaging testing?
Regulatory requirements mandate specific testing protocols to ensure compliance with ISO standards. Medical device packaging systems must meet stringent requirements for seal integrity, sterile barrier systems, and material durability to ensure the safety and effectiveness of medical devices.
- Why is process validation important in medical device packaging?
Process validation ensures that every stage of the packaging process, from sealing to labeling, consistently produces safe and effective packaging systems. This is a critical aspect of compliance with regulatory requirements and helps maintain high-quality standards across production.