Medical device packaging demands strict attention to detail, as the selection of materials influences every aspect of product safety, sterility, and regulatory compliance. For manufacturers, this process involves rigorous testing, strict adherence to industry standards, and thoughtful environmental considerations. Each element, from packaging choice to labeling, is chosen to safeguard patient health and meet healthcare requirements.
This guide provides insights into the key considerations and best practices for creating safe, effective, and sustainable packaging solutions that align with the highest standards in medical device manufacturing.
The Critical Role of Medical Device Packaging
In the medical device industry, packaging is a critical component that ensures product safety, sterility, and compliance from production to patient use. Proper packaging safeguards medical devices against contaminants, physical damage, and environmental exposure. It also maintains sterility, extends shelf life, and helps ensure that devices perform as intended, protecting both healthcare providers and patients.
Medical device packaging plays a key role in:
- Sterility and Infection Control
Maintaining a sterile barrier is essential in preventing infections and contamination. In fact, the U.S. Food and Drug Administration (FDA) mandates that all packaging for sterile medical devices meet specific microbial barrier properties under ISO 11607 standards, which help ensure that the packaging effectively prevents the ingress of microorganisms. This requirement is crucial in healthcare settings, where infections can have severe consequences (1 in 31 hospital patients suffers from at least one healthcare-associated infection). - Compliance with Regulatory Standards
The medical device industry is highly regulated to ensure product safety. Packaging must comply with standards set by organizations like the FDA and ISO, covering aspects like material durability, resistance to sterilization processes, and environmental conditions. The ISO 13485:2016 standard specifically focuses on quality management systems for medical devices, requiring manufacturers to validate packaging processes that directly impact patient safety. - Environmental and Sustainability Considerations
As sustainability becomes a priority across industries, medical device manufacturers are exploring sustainable packaging solutions. According to a 2020 survey by the Healthcare Plastics Recycling Council, over 70% of healthcare facilities see recyclability as a critical feature in purchasing decisions for medical device packaging. By selecting recyclable materials and reducing overall packaging waste, manufacturers can align with environmental and social responsibility goals while meeting compliance standards for material safety. - Product Protection and Durability
Packaging must shield medical devices from physical damage, extreme temperatures, and chemical exposure, particularly in challenging or prolonged storage conditions. Studies show that improperly protected devices can suffer a loss in sterility or functionality due to environmental exposure. - Ease of Use and Accessibility
Medical device packaging must be designed with end-users in mind, facilitating easy, sterile access to the device when needed. Features like clean peel options, ergonomic designs, and clear labeling support efficient, safe use in high-pressure environments.
Types of Medical Device Packaging Materials
Selecting the appropriate packaging materials for medical devices is a multi-layered process that requires careful consideration of each component’s role in maintaining device integrity, sterility, and functionality. Here’s a look at the primary types of packaging materials used in the medical device industry and their applications:
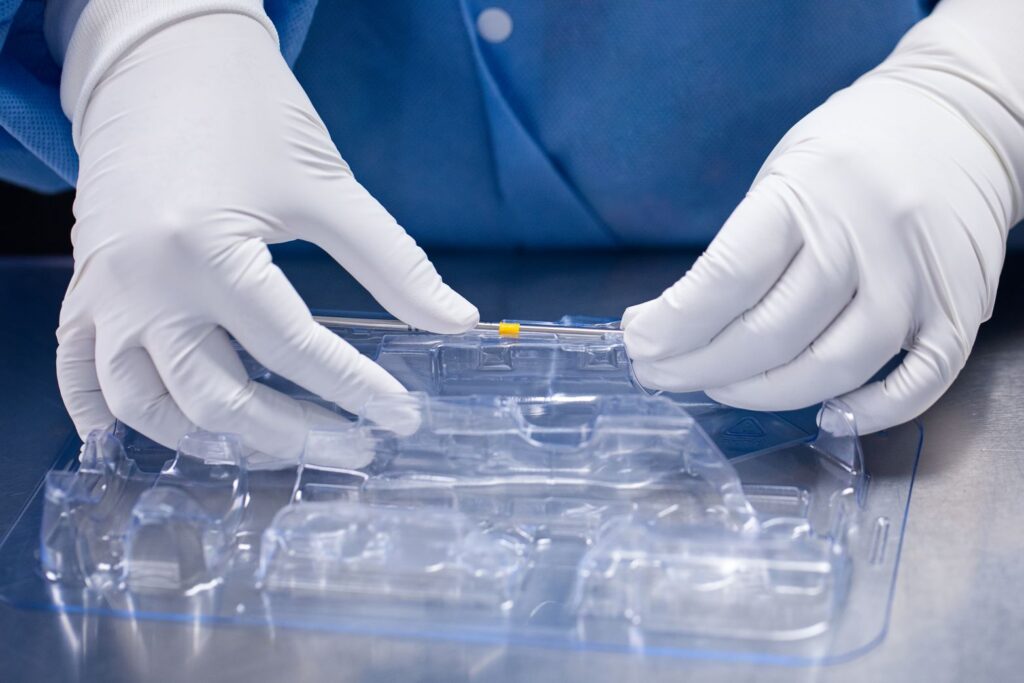
- Primary Packaging
Primary packaging is the first layer of protection that directly contains and shields the device. It is typically designed to form a robust microbial barrier and maintain sterility. Sterilization compatibility is critical here; for instance, ethylene oxide (EtO) sterilization is one of the most commonly used methods, with over 50% of U.S. medical devices sterilized this way due to its effectiveness across material types. Primary packaging materials must be compatible with the chosen sterilization process to ensure that the packaging retains its protective barrier properties after sterilization. - Secondary Packaging
Secondary packaging adds an additional layer of protection around the primary package, safeguarding it from physical impacts, environmental conditions, and handling during transportation. This packaging layer often includes cartons or boxes that reinforce the primary packaging and provide a space for product labeling and instructions. Secondary packaging must be durable enough to prevent crushing or deformation that could compromise the sterile barrier of the primary packaging. - Tertiary Packaging
Tertiary packaging is the outermost layer, essential for bulk storage, long-distance shipping, and handling. It provides structural support, stability, and protection against extreme temperatures or humidity changes during transport. Tertiary packaging is often made from sturdy materials like corrugated cardboard or reinforced boxes to withstand the rigors of distribution. - Barrier Films and Coatings
Barrier films and coatings are crucial for enhancing the microbial and chemical resistance of packaging. Advanced films, like PVDC (polyvinylidene chloride), provide excellent moisture and oxygen barriers and are widely used for sensitive devices, with a study showing that barrier films can extend the shelf life of sterile devices by up to 12 months. - Advanced Flexible Packaging
Flexible packaging solutions, such as films and foils, are commonly used for their versatility and adaptability to various device shapes. This type of packaging offers tear resistance and durability while minimizing the amount of material needed, reducing waste. Flexible packaging can also be easily customized for specific device configurations, enhancing both protective capabilities and ease of use.
Key Considerations in Selecting Packaging Materials
Selecting materials for medical device packaging requires a comprehensive understanding of the device’s specific needs and the regulatory landscape. Manufacturers must evaluate each material’s performance, compatibility with sterilization methods, and environmental impact. Key factors include:
- Sterilization Compatibility
Packaging materials must endure different sterilization methods, such as EtO, gamma irradiation, or hydrogen peroxide, without losing barrier properties or compromising material integrity. Compatibility with sterilization processes ensures that devices remain sterile and safe for use upon arrival. - Barrier Properties
Effective barrier properties are critical to prevent the ingress of contaminants like microorganisms, gasses, and moisture. Medical packaging materials are selected based on their ability to resist these external elements, ensuring product integrity over time. - Chemical and Physical Durability
Medical device packaging needs to resist chemical exposure and withstand physical handling during storage and transport. Materials with high chemical resistance are essential, as they protect against damage from sterilants and cleaning agents that could otherwise compromise packaging. - Sustainability
Environmentally friendly packaging options are becoming more important as companies aim to reduce their carbon footprint. Sustainable packaging includes recyclable, compostable, or renewable materials that align with corporate sustainability goals while still meeting medical device industry standards and patient safety requirements. - Ease of Use
Medical packaging must facilitate easy and safe access to the device for healthcare providers. Features like clean-peel designs, ergonomic shapes, and clear labeling ensure efficient and intuitive use in clinical settings.
The Packaging Process in the Medical Device Industry
When it comes to the process of creating medical device packaging itself, there are multiple stages, from initial design and material selection to manufacturing, testing, and final distribution. Each step in the process must adhere to strict regulatory guidelines to ensure the packaging meets quality, sterility, and usability requirements for healthcare settings.
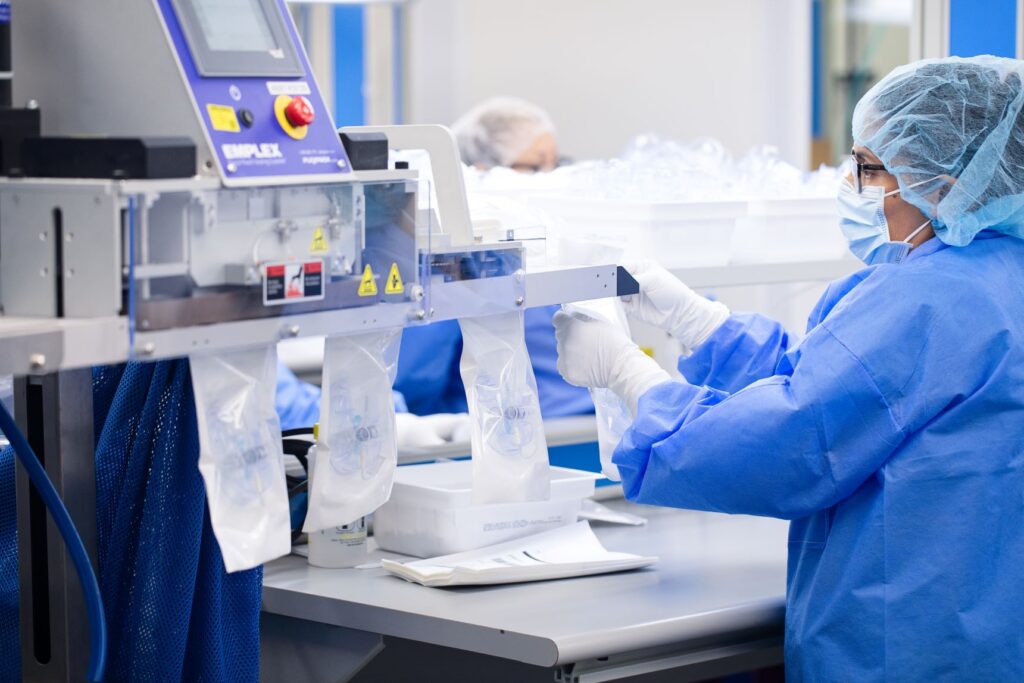
- Design and Material Selection
The first step in the packaging process involves understanding the specific requirements of the medical device. Packaging engineers work closely with the device’s design team to select packaging materials that provide the right level of protection, compatibility with sterilization methods, and usability for healthcare providers. During this phase, considerations include the device’s shape and weight, durability requirements, sterilization methods, and regulatory standards. - Prototyping and Testing
Prototyping allows manufacturers to create initial samples of the packaging design, which are then rigorously tested for durability, sterility, and barrier performance. For example, according to the ASTM F2096 standard for bubble leak testing, medical device packaging must maintain air pressure and sterility under various environmental conditions. This phase helps identify potential issues early, enabling engineers to make adjustments before full production begins. - Regulatory Compliance Checks
Before moving into production, the packaging design and materials must undergo a thorough regulatory compliance check. Compliance with FDA, ISO, and other relevant regulatory bodies ensures that the packaging meets the necessary standards for patient safety. This includes verifying labeling requirements, ensuring that materials are non-toxic and compatible with sterilization processes. - Manufacturing and Assembly
Once the design and materials are finalized and approved, the packaging moves into full-scale production. This stage involves creating the primary, secondary, and tertiary packaging layers and assembling them as needed. Manufacturing processes are closely monitored to maintain quality, ensuring that each package produced meets the required standards for durability, sterility, and performance. - Sterilization and Quality Assurance
After manufacturing, most medical device packaging undergoes sterilization using methods like EtO, gamma irradiation, or hydrogen peroxide, depending on the device’s requirements. Quality assurance teams then inspect and test the packaging to ensure it maintains a sterile barrier and that the sterilization process does not compromise the material’s integrity. This step is essential to ensure that devices are safe and ready for use upon reaching healthcare facilities. - Labeling and Instructions for Use
Proper labeling is crucial for compliance and usability. Labels must clearly display the device name, sterilization method, expiration date, and instructions for opening. Instructions for use and handling are also included to guide healthcare providers on how to safely and efficiently access the device without compromising sterility. This information is vital in ensuring patient safety and regulatory compliance. - Distribution and Storage
The final step in the packaging process involves preparing the packaged devices for distribution. Tertiary packaging is typically used to protect devices during transport, ensuring that the primary and secondary packaging layers remain intact. Proper storage conditions, including temperature and humidity control, are maintained during distribution to prevent degradation of materials or sterility. The packaging is designed to maintain its protective properties throughout the device’s shelf life.
Ensuring Quality and Safety Through Ongoing Monitoring
Continuous monitoring is required to ensure that packaging performs as intended over time and under various conditions. Manufacturers often conduct ongoing audits, quality checks, and environmental monitoring to ensure that the packaging continues to meet all regulatory requirements and maintains its protective properties. Here are key practices manufacturers use to ensure that packaging performs reliably in diverse and sometimes challenging environments:
- Post-Market Surveillance
Once the device is on the market, companies engage in post-market surveillance to monitor the packaging’s performance under real-world conditions. This data helps identify any unforeseen issues that could arise from handling, transport, or storage. Adjustments based on this feedback allow manufacturers to improve packaging designs or materials, enhancing future product reliability. - Environmental Monitoring
To ensure that packaging remains effective, environmental monitoring programs test packaging resilience to various storage and transport conditions, such as temperature extremes, humidity, and exposure to light. Regular testing and monitoring help confirm that packaging materials are capable of withstanding diverse environmental stresses. - Routine Quality Audits
Routine quality audits and compliance checks are conducted to verify that manufacturing processes continue to meet regulatory standards. As per FDA guidelines, manufacturers must audit their processes and report findings to ensure compliance, reducing the likelihood of device recalls. These audits involve checking durability, labeling accuracy, barrier integrity, and sterility retention. Regular quality checks are essential in maintaining high standards and regulatory compliance, reducing the risk of product recalls or regulatory concerns. - Customer and Healthcare Provider Feedback
Gathering feedback from healthcare providers who use the packaging daily provides insight into the packaging’s usability and performance. This feedback helps manufacturers address any issues related to ease of access, labeling clarity, or durability, allowing for improvements that benefit the healthcare professionals and patients who rely on these products. - Periodic Shelf-Life Testing
Shelf-life testing assesses the packaging’s durability and sterility over its intended storage period. Packaging that can maintain a sterile barrier and withstand environmental changes throughout its expected shelf life ensures that devices are safe for use up to their expiration date. Shelf-life testing also supports accurate labeling, providing healthcare providers with essential information on product safety and usability. - Commitment to Innovation and Continuous Improvement
Manufacturers who continuously seek innovative materials and designs are better able to meet the evolving needs of the healthcare industry. Whether integrating smart technology, improving sustainability, or enhancing barrier properties, the focus on continuous improvement ensures that packaging solutions remain safe, effective, and aligned with industry trends.
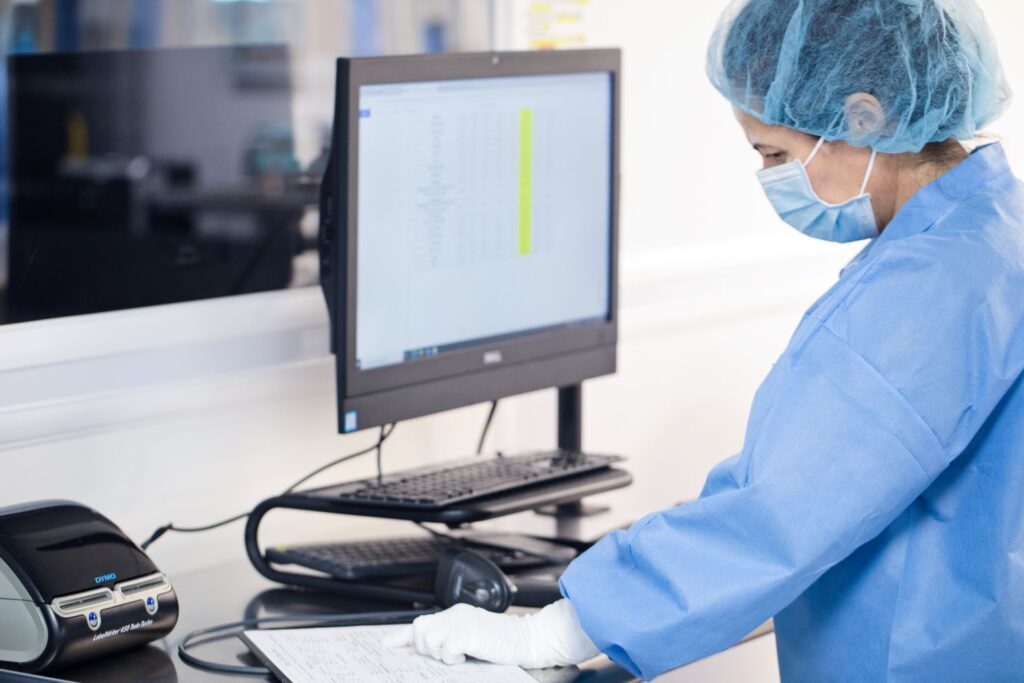
Conclusion
In the world of medical device packaging, experience isn’t just a competitive advantage; it’s a crucial component of patient care and healthcare integrity. The right packaging solution has the potential to bridge clinical precision with effective safety practices, offering protection and reliability without compromising patient safety. Packaging must not only shield devices from contaminants but also integrate seamlessly into clinical workflows, enhance user safety, and adapt to rapid advancements in healthcare technology. For forward-thinking manufacturers, the journey involves embracing a multifaceted approach—prioritizing regulatory compliance, environmental impact, usability, and technological innovation. It’s a forward-looking responsibility that pushes the industry to meet current needs and anticipate future healthcare challenges.
As packaging continues to adapt and evolve, it will become more than just an outer layer of protection; it will embody a promise of safety, precision, and usability, ultimately serving as a foundational element in the trust and care patients expect from modern healthcare solutions.
FAQs
- What are the essential factors in choosing packaging materials for medical devices?
Selecting the right packaging materials requires careful consideration of regulatory standards, barrier properties, sterilization compatibility, and sustainability goals. Additionally, the packaging must support the device’s usability and maintain its integrity across diverse handling and storage conditions.
- Why is sterile packaging critical in the healthcare industry?
Sterile packaging protects medical devices from contamination, ensuring aseptic presentation and safeguarding patient health. Without sterile packaging, devices could introduce infections, posing significant risks to both patients and healthcare providers.
- What testing is involved in medical device packaging?
Testing includes integrity tests for durability, microbial barrier performance, and resistance to sterilization processes like gamma irradiation and EtO sterilization. These tests ensure that the packaging can maintain its protective qualities throughout the product’s lifecycle, even under challenging conditions.
- What is the role of tertiary packaging in medical device shipping?
Tertiary packaging provides additional protection during transport, especially for long-distance or bulk shipments in extreme conditions. This outer layer helps prevent damage from impact, moisture, or temperature changes, ensuring the safe arrival of medical devices.
- Why is chemical resistance important in medical device packaging?
Chemical resistance is crucial because packaging must withstand exposure to sterilizing agents, ensuring it remains effective and intact. Without this property, packaging materials could degrade, compromising the sterility and safety of the device within.